¿Qué es un sistema de llenado?
Un sistema de llenado es una máquina o grupo de máquinas que se utilizan para envasar y llenar un determinado producto en recipientes o envases. Los sistemas de llenado se utilizan en una amplia gama de industrias, como la alimentaria y de bebidas, la farmacéutica, la química y la de productos de consumo.
Hay muchos tipos diferentes de sistemas de llenado, cada uno diseñado para manipular tipos específicos de productos y materiales de envasado. Algunos tipos comunes de sistemas de llenado incluyen:
Sistemas de llenado de líquidos: Estos sistemas se utilizan para llenar productos líquidos, como bebidas, salsas y productos de limpieza, en recipientes como botellas, latas y bolsas.
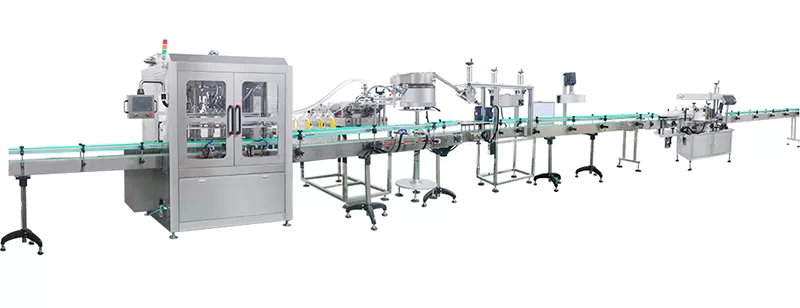
Sistemas de llenado de polvo: estos sistemas se utilizan para llenar productos secos en polvo, como especias, harina y detergentes, en contenedores como bolsas, botellas y cajas.
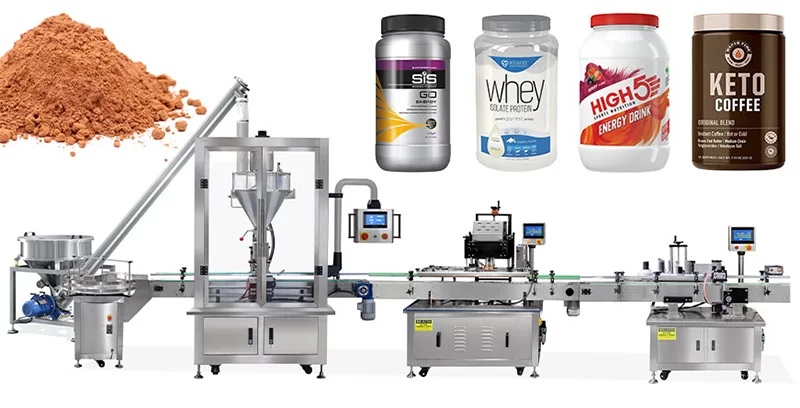
Sistemas de llenado sólido: estos sistemas se utilizan para llenar productos sólidos, como dulces, tabletas y gomitas, en recipientes como bolsas, cajas y frascos.
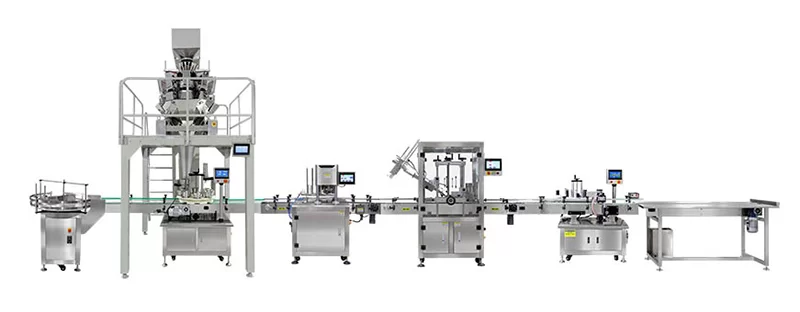
Sistemas de llenado de semisólidos: estos sistemas se utilizan para llenar productos semisólidos, como cremas, pastas y geles, en recipientes como tubos, botellas y frascos.
Los sistemas de llenado generalmente consisten en una serie de máquinas que trabajan juntas para envasar el producto, incluidos transportadores, máquinas llenadoras, etiquetadoras, tapadoras y envasadoras. Algunos sistemas de llenado también están equipados con sistemas de control de calidad para garantizar que el producto se llene de manera precisa y consistente.
¿Cuáles son los diferentes tipos de sistemas de llenado disponibles?
Hay muchos tipos diferentes de sistemas de llenado disponibles, y el mejor sistema para una aplicación en particular dependerá de los requisitos específicos del producto que se llena y los materiales de empaque que se utilizan. Algunos tipos comunes de sistemas de llenado incluyen:
Llenadoras por gravedad: Estos sistemas utilizan la gravedad para dispensar el producto en el envase del envase. Por lo general, se usan para líquidos de baja viscosidad y son muy adecuados para llenar grandes volúmenes a un costo relativamente bajo.
Llenadoras a presión: Estos sistemas utilizan presión para dispensar el producto en el envase del envase. Por lo general, se usan para líquidos de mayor viscosidad y son muy adecuados para llenar pequeños volúmenes con alta precisión.
Llenadoras de pistón: Estos sistemas utilizan un pistón para dispensar el producto en el envase del envase. Por lo general, se usan para líquidos de viscosidad media a alta y son adecuados para llenar volúmenes pequeños a medianos con alta precisión.
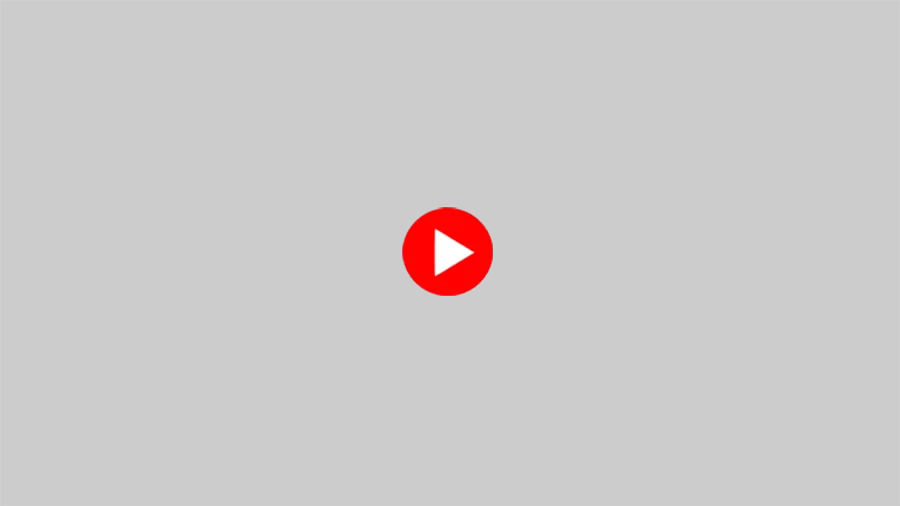
Línea de sistema de llenado de botellas pequeñas
Llenadoras de barrena: estos sistemas utilizan una barrena o un tornillo para dispensar el producto en el contenedor de embalaje. Por lo general, se usan para productos secos en polvo y son muy adecuados para llenar volúmenes pequeños a medianos con alta precisión.
Llenadoras de peso neto: estos sistemas utilizan una báscula para dispensar el producto en el contenedor de embalaje. Por lo general, se usan para productos granulares secos y son adecuados para llenar volúmenes pequeños a grandes con alta precisión.
Llenadoras volumétricas: Estos sistemas utilizan un dispositivo de medición para dispensar el producto en el envase del envase. Por lo general, se usan para líquidos, pastas y productos semisólidos y son adecuados para llenar volúmenes medianos a grandes con una precisión moderada.
¿Qué factores se deben considerar al seleccionar un sistema de llenado?
Hay varios factores a considerar al seleccionar un sistema de llenado, incluyendo:
Características del producto: El tipo de producto que se llena, incluida su viscosidad, densidad, pH y potencial de formación de espuma o derrames, influirá en el tipo de sistema de llenado más apropiado.
Materiales de empaque: El tipo de material de empaque que se utilice, incluido su tamaño, forma y compatibilidad con el producto, también influirá en el tipo de sistema de llenado más apropiado.
Volumen de producción: el volumen de producto que debe llenarse afectará el tamaño y la capacidad del sistema de llenado requerido.
Exactitud y precisión: El nivel de exactitud y precisión requerido para el llenado del producto influirá en el tipo de sistema de llenado más adecuado.
Costo: El costo del sistema de llenado, incluido el precio de compra inicial y los costos operativos y de mantenimiento continuos, también será un factor en el proceso de selección.
Restricciones de espacio: el espacio disponible para el sistema de llenado también será un factor en el proceso de selección, ya que algunos sistemas pueden requerir más espacio que otros.
Seguridad: La seguridad del sistema de llenado, incluida la posibilidad de derrames o fugas, también será un factor en el proceso de selección.
Facilidad de uso y mantenimiento: La facilidad de uso y mantenimiento del sistema de llenado también serán consideraciones importantes, así como la disponibilidad de soporte técnico y capacitación.
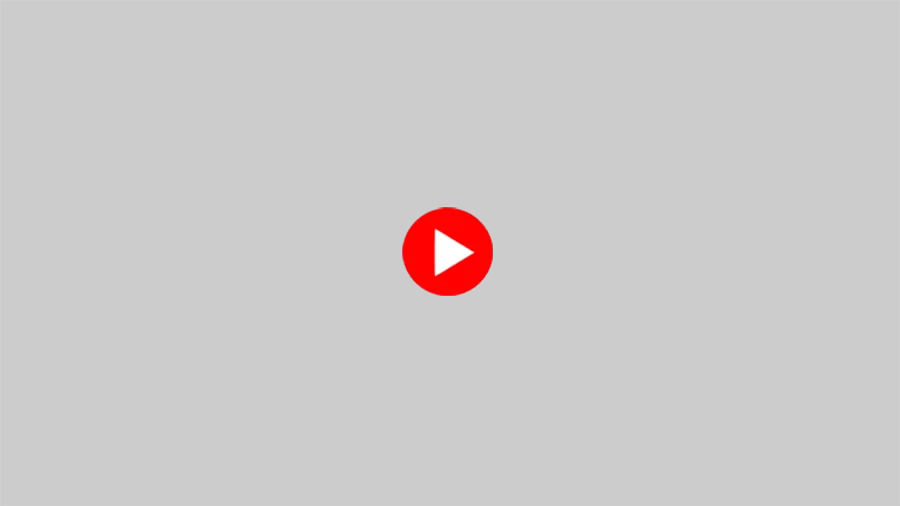
Línea de sistema de llenado de botellas cuadradas
¿Cómo funciona un sistema de llenado?
El proceso específico de funcionamiento de un sistema de llenado dependerá del tipo de sistema de llenado que se utilice y de las características del producto que se esté llenando. Sin embargo, la mayoría de los sistemas de llenado siguen un proceso básico similar:
Preparación: El producto y los materiales de empaque se preparan para el llenado. Esto puede implicar calentar o enfriar el producto, esterilizar los materiales de empaque y configurar la máquina de llenado.
Llenado: El producto se dosifica en el recipiente de envasado utilizando el método de llenado adecuado, como el llenado por gravedad, el llenado a presión o el llenado volumétrico.
Tapado: El envase del envase se sella con una tapa o cierre, como una tapa de rosca o una tapa a presión.
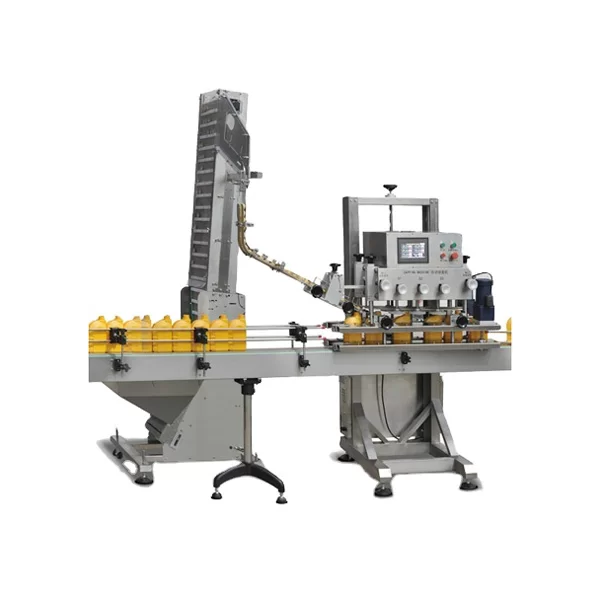
Etiquetado: el envase del empaque está etiquetado con información del producto, como el nombre, los ingredientes y la fecha de vencimiento.
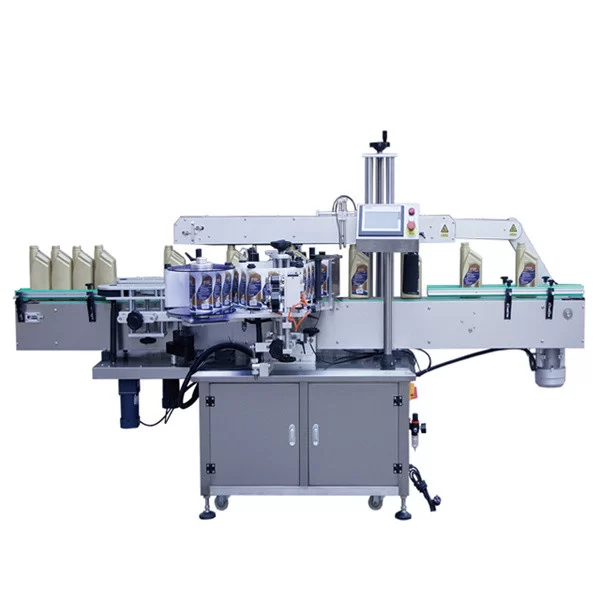
Control de calidad: se inspecciona la precisión y la calidad del producto lleno y empacado, y cualquier producto defectuoso se retira de la línea de producción.
Empaque: El producto terminado se empaqueta para su envío o almacenamiento. Esto puede implicar empacar o embolsar el producto, o colocarlo en una tarima para su transporte.
Los sistemas de llenado se pueden automatizar total o parcialmente, según la complejidad del proceso y el volumen de producto que se produzca. Algunos sistemas de llenado también pueden incluir pasos adicionales, como pasteurización o esterilización, según el producto y los requisitos de la aplicación.
¿Cuáles son los componentes del sistema de llenado?
Los componentes específicos de un sistema de llenado dependerán del tipo de sistema de llenado que se utilice y de las características del producto que se esté llenando. Sin embargo, la mayoría de los sistemas de llenado incluirán los siguientes componentes:
Transportador: Se utiliza un transportador para transportar el producto y los materiales de empaque a través del sistema de llenado.
Máquina llenadora: La máquina llenadora se encarga de dispensar el producto en el envase del envase. Puede ser una llenadora por gravedad, una llenadora a presión, una llenadora volumétrica u otro tipo de máquina llenadora.
Taponadora: La taponadora se encarga de sellar el envase del envase con una tapa o cierre.
Etiquetadora: La etiquetadora se encarga de aplicar las etiquetas al envase del envase.
Sistema de control de calidad: se puede utilizar un sistema de control de calidad para inspeccionar la precisión y la calidad del producto lleno y envasado, y para eliminar cualquier producto defectuoso de la línea de producción.
Máquina empacadora: se puede usar una máquina empacadora para empacar el producto terminado para su envío o almacenamiento, como empacar o embolsar el producto, o colocarlo en una tarima.
Además de estos componentes principales, un sistema de llenado también puede incluir otros equipos auxiliares, como bombas, intercambiadores de calor y equipos de esterilización, según los requisitos específicos de la aplicación.
¿Cuáles son las ventajas y desventajas de los diferentes sistemas de llenado?
Las ventajas y desventajas de los diferentes sistemas de llenado dependerán de las características específicas del producto que se llena y los requisitos de la aplicación. Aquí hay algunas ventajas y desventajas generales de algunos tipos comunes de sistemas de llenado:
Llenadoras por gravedad:
- Ventajas: bajo costo, operación simple, bajo mantenimiento
- Desventajas: limitado a líquidos de baja viscosidad, baja exactitud y precisión
Llenadoras a presión:
- Ventajas: Alta exactitud y precisión, adecuado para líquidos de alta viscosidad.
- Desventajas: Mayor costo, operación y mantenimiento más complejo
Llenadoras de pistón:
- Ventajas: Alta exactitud y precisión, adecuado para líquidos de viscosidad media a alta
- Desventajas: Mayor costo, operación y mantenimiento más complejo
Llenadoras de barrena:
- Ventajas: Alta exactitud y precisión, adecuado para productos secos y en polvo
- Desventajas: Mayor costo, operación y mantenimiento más complejo, limitado a productos secos
Llenadoras de peso neto:
- Ventajas: alta exactitud y precisión, adecuado para productos líquidos, pastosos, secos y granulares
- Desventajas: Mayor costo, operación y mantenimiento más complejo
Llenadoras volumétricas:
- Ventajas: Exactitud y precisión moderadas, adecuado para líquidos, pastas y productos semisólidos
- Desventajas: Exactitud y precisión limitadas, operación y mantenimiento más complejos
¿Cómo se mantiene y se solucionan los problemas de un sistema de llenado?
El mantenimiento y la resolución de problemas adecuados de un sistema de llenado son importantes para garantizar que funcione con eficacia y produzca productos de alta calidad. Estas son algunas pautas generales para el mantenimiento y la resolución de problemas de un sistema de llenado:
Siga un programa de mantenimiento regular: Establezca un programa de mantenimiento periódico y sígalo al pie de la letra para asegurarse de que todos los componentes del sistema de llenado funcionan correctamente. Esto puede incluir la limpieza y lubricación de la maquinaria, la sustitución de piezas desgastadas o dañadas y la calibración del equipo.
Mantenga registros precisos: Mantenga registros precisos de todos los trabajos de mantenimiento y reparación, incluida la fecha, el alcance del trabajo y las piezas sustituidas. Esto ayudará a identificar tendencias y posibles problemas con el sistema de llenado.
Supervise de cerca el proceso de llenado: Preste mucha atención al proceso de llenado y controle si se producen ruidos, vibraciones u otros problemas inusuales que puedan indicar un problema con la maquinaria.
Compruebe si hay fugas y derrames: Inspeccione regularmente el sistema de llenado en busca de fugas y derrames, y tome medidas inmediatas para solucionar cualquier problema que se identifique.
Mantenga limpio el sistema de llenado: Mantenga el sistema de llenado y sus alrededores limpios y libres de residuos para evitar la contaminación del producto.
Siga las directrices de seguridad: Siga siempre las directrices de seguridad cuando trabaje en el sistema de llenado, incluido el uso de ropa y equipos de protección y el cumplimiento de los procedimientos adecuados de bloqueo y etiquetado.
Busque la ayuda de un experto: Si no puede identificar o solucionar un problema con el sistema de llenado, solicite la ayuda de un técnico cualificado o de un proveedor de servicios.
¿Cuáles son las consideraciones de seguridad al utilizar un sistema de llenado?
Hay varias consideraciones de seguridad que deben tenerse en cuenta al utilizar un sistema de llenado:
Siga las directrices de seguridad adecuadas: Siga todas las directrices y procedimientos de seguridad al utilizar y mantener el sistema de llenado, incluyendo el uso de ropa y equipos de protección adecuados y el cumplimiento de los procedimientos de bloqueo/etiquetado.
Tenga cuidado al manipular materiales peligrosos: Si el producto que se está llenando es peligroso o potencialmente peligroso, tome las precauciones adecuadas para garantizar su seguridad y la de los demás. Esto puede incluir el uso de barreras o recintos de protección, el suministro de equipos de protección personal y el seguimiento de los procedimientos adecuados de manipulación y eliminación.
Inspeccione regularmente el sistema de llenado: Inspeccione periódicamente el sistema de llenado para detectar cualquier signo de daño o desgaste, y tome medidas inmediatas para solucionar cualquier problema que se identifique.
Mantenga limpio el sistema de llenado: Mantenga el sistema de llenado y sus alrededores limpios y libres de residuos para evitar la contaminación del producto.
Utilice una ventilación adecuada: Si el producto que se está llenando genera humos o vapores, asegúrese de que existe una ventilación adecuada para evitar la acumulación de gases peligrosos.
Siga los procedimientos de emergencia adecuados: Familiarícese con los procedimientos de parada de emergencia del sistema de llenado y sepa cómo utilizar el botón de parada de emergencia en caso de emergencia.
Busque la ayuda de un experto: Si no está seguro de cómo utilizar o mantener el sistema de llenado de forma segura, solicite la ayuda de un técnico cualificado o de un proveedor de servicios.
¿Cómo se calculan el caudal y la velocidad de llenado de un sistema de llenado?
El caudal y la velocidad de llenado de un sistema de llenado pueden calcularse mediante las siguientes fórmulas:
Caudal = volumen de producto llenado / tiempo de llenado
Velocidad de llenado = número de envases llenados / tiempo de llenado
Para calcular el caudal, deberá medir el volumen de producto que se llena en el envase y el tiempo que se tarda en llenar ese volumen. Para calcular la velocidad de llenado, tendrá que contar el número de envases que se llenan y el tiempo que se tarda en llenarlos.
Por ejemplo, si está llenando 1 litro de producto en botellas y tarda 30 segundos en llenar cada botella, el caudal sería 1 litro / 0,5 minutos = 2 litros/minuto y la velocidad de llenado sería 1 botella / 0,5 minutos = 2 botellas/minuto.
Es importante tener en cuenta que el caudal y la velocidad de llenado de un sistema de llenado pueden verse afectados por una serie de factores, como la viscosidad del producto, el tamaño y la forma del envase y el tipo de máquina de llenado utilizada. Puede ser necesario ajustar el proceso de llenado o el equipo de llenado para conseguir el caudal y la velocidad de llenado deseados.
¿Cuáles son los requisitos reglamentarios de los sistemas de llenado?
Hay una serie de requisitos normativos que pueden aplicarse a los sistemas de llenado, dependiendo de la industria específica y del tipo de producto que se llene. Algunos de los requisitos normativos más comunes son
Buenas prácticas de fabricación (BPF):
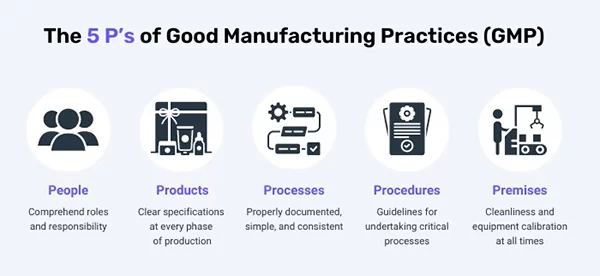
Muchas industrias, incluidas la alimentaria, la farmacéutica y la cosmética, están obligadas a seguir las directrices de las GMP a la hora de diseñar y utilizar sistemas de llenado. Estas directrices ofrecen recomendaciones sobre el diseño, la construcción y el funcionamiento de los sistemas de llenado para garantizar la seguridad y la calidad del producto.
Análisis de peligros y puntos de control crítico (APPCC):
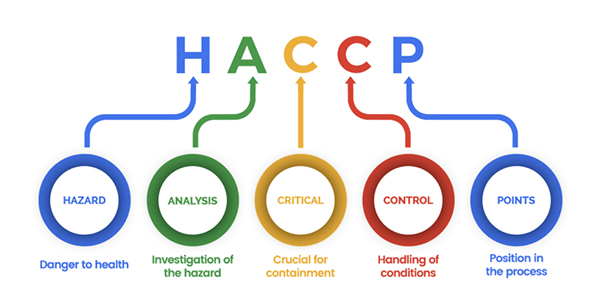
Las industrias que producen alimentos y bebidas pueden estar obligadas a seguir las directrices HACCP a la hora de diseñar y operar sistemas de llenado. Las directrices HACCP ofrecen recomendaciones para identificar y controlar los peligros potenciales en el proceso de producción, incluidos el diseño y el funcionamiento de los sistemas de llenado.
Normativa de la Administración de Alimentos y Medicamentos (FDA):
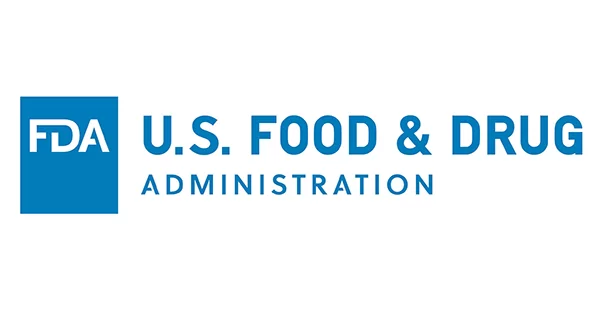
Las industrias que fabrican alimentos, bebidas y productos farmacéuticos pueden estar sujetas a la normativa de la FDA, que incluye requisitos específicos para el diseño y el funcionamiento de los sistemas de llenado.
Normativa de la Administración de Seguridad y Salud en el Trabajo (OSHA):
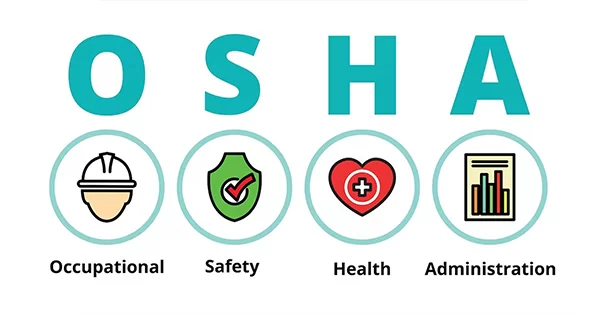
Las industrias de Estados Unidos están sujetas a la normativa de la OSHA, que incluye requisitos específicos para la seguridad de los sistemas de llenado, incluido el uso de equipos de protección, guardias de seguridad y procedimientos de parada de emergencia.
Normativa medioambiental:
Las industrias también pueden estar sujetas a normativas medioambientales, que pueden incluir requisitos específicos para el diseño y funcionamiento de los sistemas de llenado con el fin de minimizar el impacto sobre el medio ambiente, como la correcta eliminación de materiales peligrosos.
Es importante consultar con los organismos reguladores y los expertos del sector para determinar los requisitos normativos específicos que se aplican a su sistema de llenado. El incumplimiento de estos requisitos puede dar lugar a multas, acciones legales y daños a su reputación.
¿Cómo puedo optimizar la eficiencia de mi sistema de llenado?
Hay varias formas de optimizar la eficiencia de un sistema de llenado, entre ellas:
Mantenimiento regular:
Asegurarse de que el sistema de llenado se mantiene correctamente y en buen estado de funcionamiento puede ayudar a optimizar su eficiencia. Esto puede incluir la limpieza y lubricación de la maquinaria, la sustitución de piezas desgastadas o dañadas y la calibración del equipo.
Optimización del proceso:
Optimizar el propio proceso de llenado puede ayudar a mejorar la eficiencia. Esto puede incluir el ajuste de la velocidad de llenado, el ajuste del caudal del producto o el uso de una boquilla o método de llenado diferentes.
Formación y supervisión:
Proporcionar una formación y supervisión adecuadas a los operarios puede ayudar a garantizar que el sistema de llenado se utiliza de forma correcta y eficiente.
Automatización:
La automatización de ciertos aspectos del proceso de llenado, como el taponado y el etiquetado, puede ayudar a optimizar la eficiencia.
Técnicas de fabricación ajustada:
La aplicación de técnicas de fabricación ajustada, como la reducción de residuos y la optimización del flujo de materiales, puede ayudar a mejorar la eficiencia del sistema de llenado.
Diseño del producto y del envase:
Optimizar el diseño del producto y del envase puede ayudar a mejorar la eficiencia en el proceso de llenado. Por ejemplo, el uso de materiales de envasado que sean más fáciles de llenar o que requieran menos producto para el llenado puede mejorar la eficiencia.
Actualización de equipos:
Actualizar o sustituir el equipo antiguo o ineficiente también puede ayudar a optimizar la eficiencia del sistema de llenado.
Es importante evaluar periódicamente la eficiencia del sistema de llenado e identificar áreas de mejora. Esto puede implicar el análisis de los datos de producción, la observación del proceso de llenado y la consulta con expertos para identificar posibles áreas de optimización.
¿Cuál es la precisión del sistema de llenado en términos de volumen o peso de llenado?
La precisión de un sistema de llenado en términos de volumen o peso dependerá de una serie de factores, como el tipo específico de sistema y boquilla de llenado que se utilice, las características del producto a llenar y los requisitos de la aplicación. A continuación se ofrecen algunas directrices generales sobre la precisión de los distintos tipos de sistemas de llenado:
Llenadoras por gravedad: Estos sistemas no suelen ser muy precisos y pueden tener un rango de precisión de hasta +/- 5%.
Llenadoras a presión: Estos sistemas suelen ser más precisos que las llenadoras por gravedad y pueden tener un rango de precisión de hasta +/- 2%.
Llenadoras de pistón: Estos sistemas suelen ser muy precisos y pueden tener un margen de precisión de hasta +/- 1%.
Llenadoras de tornillo sinfín: Estos sistemas suelen ser muy precisos y pueden tener un margen de precisión de hasta +/- 1%.
Llenadoras de peso neto: Estos sistemas suelen ser muy precisos y pueden tener un margen de precisión de hasta +/- 0,1%.
Llenadoras volumétricas: Estos sistemas suelen ser menos precisos que otros tipos de sistemas de llenado y pueden tener un rango de precisión de hasta +/- 5%.
Es importante señalar que la precisión de un sistema de llenado puede verse afectada por una serie de factores, como la viscosidad del producto, el tamaño y la forma del recipiente de envasado y el estado de la maquinaria de llenado. Puede ser necesario ajustar el proceso de llenado o la maquinaria de llenado para alcanzar el nivel de precisión deseado.
¿Es compatible el sistema de llenado con otros equipos de la cadena de producción?
La compatibilidad de un sistema de llenado con otros equipos de la línea de producción dependerá de las características específicas del sistema de llenado y de los otros equipos. En general, es importante asegurarse de que el sistema de llenado es compatible con los materiales de envasado y la maquinaria de envasado utilizados, así como con cualquier otro equipo con el que el producto llenado vaya a entrar en contacto, como cintas transportadoras, etiquetadoras y paletizadores.
Para garantizar la compatibilidad, es importante considerar detenidamente el diseño y el funcionamiento del sistema de llenado y cómo interactuará con los demás equipos de la línea de producción. Esto puede implicar consultar con fabricantes de equipos o especialistas para identificar posibles problemas de compatibilidad y desarrollar un plan para resolverlos.
En algunos casos, puede ser necesario realizar modificaciones en el sistema de llenado o en otros equipos para garantizar la compatibilidad. También es importante asegurarse de que el sistema de llenado está correctamente integrado en la línea de producción y de que los operarios reciben la formación y supervisión adecuadas para garantizar un funcionamiento seguro y eficaz.
¿Cuál es el coste del sistema de llenado y cómo se compara con otras opciones?
El coste de un sistema de llenado dependerá de varios factores, como el tipo específico de sistema y boquilla de llenado que se utilice, el tamaño y la capacidad del sistema, la complejidad del proceso de llenado y los requisitos específicos de la aplicación. En general, los sistemas de llenado pueden costar desde unos pocos miles de dólares para una llenadora sencilla hasta varios cientos de miles de dólares para un sistema de llenado totalmente automatizado con funciones avanzadas.
Para comparar el coste de las distintas opciones de sistemas de llenado, es importante tener en cuenta el coste total de propiedad, incluido el precio de compra inicial, los costes de instalación, los costes operativos y de mantenimiento en curso, y cualquier posible actualización o modificación que pueda ser necesaria. También es importante tener en cuenta el posible rendimiento de la inversión (ROI) del sistema de llenado, incluido el posible ahorro de costes y el aumento de la eficiencia que puede proporcionar.
En algunos casos, puede resultar más rentable adquirir un sistema de llenado usado o alquilar un sistema de llenado a corto plazo que comprar un sistema nuevo. Es importante considerar detenidamente las necesidades y objetivos específicos del sistema de llenado y consultar con expertos para determinar la opción más rentable.
¿De qué nivel de asistencia técnica dispone el sistema de llenado?
El nivel de asistencia técnica disponible para un sistema de llenado dependerá del fabricante o proveedor específico del sistema. En general, los fabricantes y proveedores de equipos de llenado suelen ofrecer una serie de servicios de asistencia técnica, entre los que se incluyen:
Documentación técnica:
Muchos fabricantes y proveedores proporcionan documentación técnica detallada, incluidos manuales de instalación y funcionamiento, guías de mantenimiento y guías de solución de problemas, para ayudar a los usuarios a comprender y utilizar el sistema de llenado.
Asistencia telefónica y en línea:
Muchos fabricantes y proveedores ofrecen asistencia telefónica y en línea para ayudar a los usuarios a solucionar problemas y responder preguntas sobre el sistema de llenado.
Asistencia in situ:
Algunos fabricantes y proveedores ofrecen asistencia in situ, incluidos servicios de instalación, mantenimiento y reparación, para ayudar a los usuarios a optimizar el rendimiento del sistema de llenado.
Formación:
Muchos fabricantes y proveedores ofrecen programas de formación para ayudar a los usuarios a comprender el funcionamiento y el mantenimiento del sistema de llenado.
Piezas de repuesto:
Muchos fabricantes y proveedores ofrecen una gama de piezas de repuesto para ayudar a los usuarios a mantener y reparar el sistema de llenado.
Es importante considerar detenidamente el nivel de asistencia técnica disponible para el sistema de llenado y asegurarse de que el fabricante o proveedor es capaz de satisfacer las necesidades y requisitos específicos de la aplicación. También es una buena idea establecer una relación con el fabricante o proveedor y desarrollar un plan de asistencia técnica y mantenimiento continuos.
¿Cuáles son los distintos tipos de válvulas de llenado y cómo funcionan?
Existen varios tipos de válvulas de llenado que se utilizan en los sistemas de llenado para controlar el flujo del producto que se está llenando. He aquí algunos tipos comunes de válvulas de llenado y una breve descripción de su funcionamiento:
Válvulas de bola: Estas válvulas utilizan una bola giratoria con un orificio en el centro para controlar el flujo del producto. Cuando la bola está alineada con la trayectoria del flujo, el producto puede fluir a través de la válvula. Cuando la bola gira para bloquear el paso del caudal, el flujo del producto se detiene.
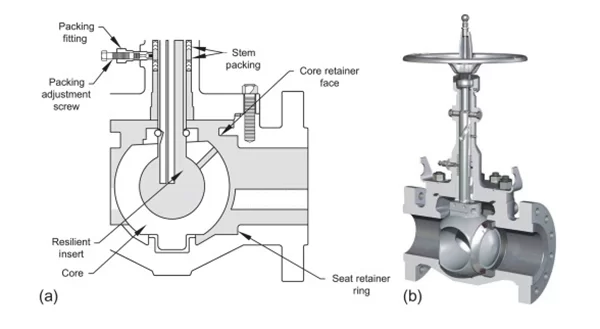
Válvulas de diafragma: Estas válvulas utilizan un diafragma flexible para controlar el flujo del producto. Cuando se presiona el diafragma contra una abertura, se detiene el flujo del producto. Cuando el diafragma se separa de la abertura, el flujo del producto pasa a través de la válvula.
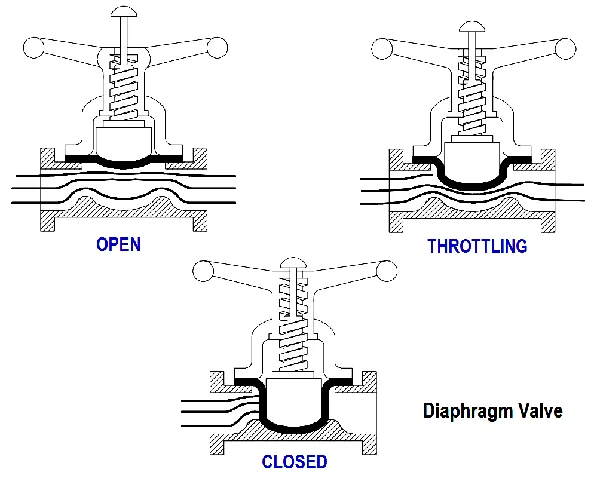
Válvulas de compuerta: Estas válvulas utilizan una compuerta o cuña para controlar el flujo del producto. Cuando la compuerta está alineada con la trayectoria del flujo, el producto puede fluir a través de la válvula. Cuando la compuerta se gira para bloquear el paso del caudal, el flujo del producto se detiene.
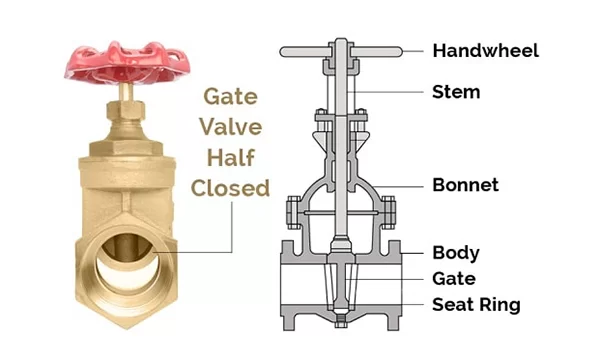
Válvulas de globo: Estas válvulas utilizan un disco móvil para controlar el flujo del producto. Cuando el disco se presiona contra una abertura, se detiene el flujo del producto. Cuando el disco se retira de la abertura, el flujo del producto pasa a través de la válvula.
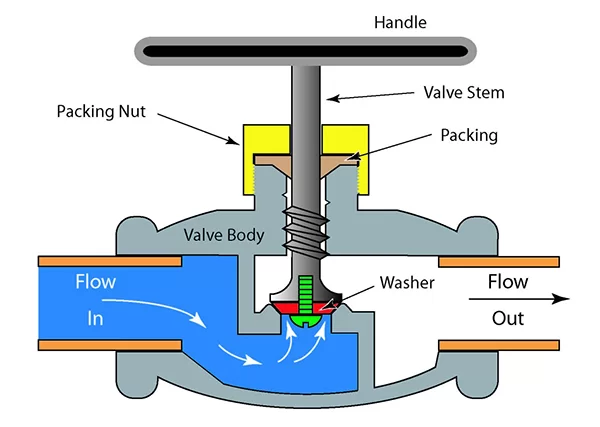
Válvulas de aguja: Estas válvulas utilizan un vástago en forma de aguja para controlar el flujo del producto. Cuando se presiona el vástago contra una abertura, se detiene el flujo del producto. Cuando el vástago se separa de la abertura, el flujo del producto pasa a través de la válvula.
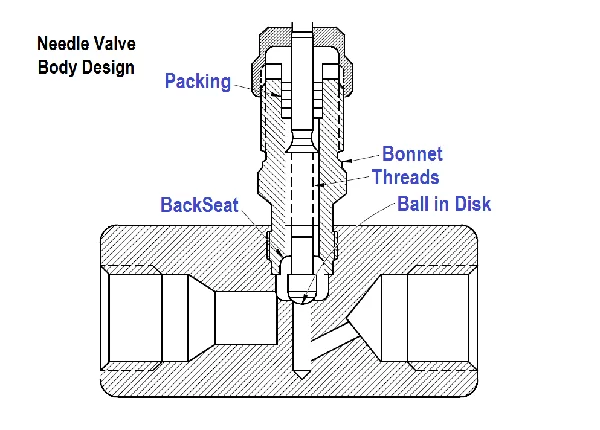
Válvulas de tapón: Estas válvulas utilizan un tapón o cilindro para controlar el flujo del producto. Cuando se gira el obturador para alinearlo con el paso del caudal, el producto puede fluir a través de la válvula. Cuando el tapón se gira para bloquear el paso del caudal, el flujo del producto se detiene.
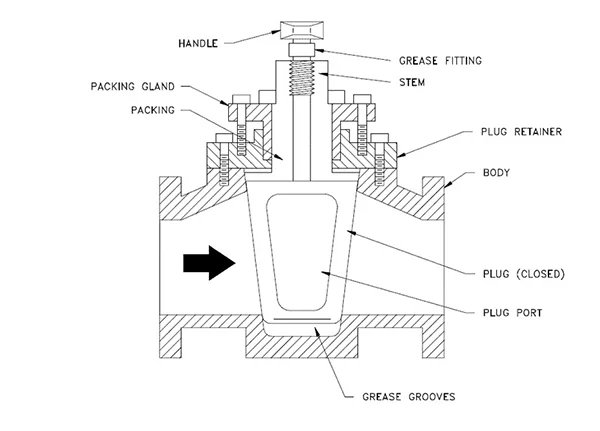
El tipo específico de válvula de llenado que se utiliza en un sistema de llenado dependerá de las características específicas del producto que se está llenando y de los requisitos de la aplicación.
¿Cómo calibro mi sistema de llenado?
Calibrar un sistema de llenado implica ajustar el proceso o el equipo de llenado para garantizar que se dispensa el volumen o el peso correctos del producto. A continuación se indican algunos pasos generales para calibrar un sistema de llenado:
Determine el volumen o peso de llenado deseado: El primer paso para calibrar un sistema de llenado es determinar el volumen o peso de llenado deseado. Esto puede basarse en las especificaciones del producto o envase, los requisitos normativos o los requisitos del cliente.
Recopilar y analizar datos: El siguiente paso consiste en recopilar datos sobre el proceso de llenado, como la velocidad de llenado, el caudal y el volumen o peso dispensado. Estos datos pueden utilizarse para identificar cualquier desviación del volumen o peso de llenado deseado y determinar la causa de la desviación.
Ajuste el proceso o el equipo de llenado: Una vez identificada la causa de la desviación, se puede ajustar el proceso o el equipo de llenado para corregirla. Esto puede implicar ajustar la velocidad de llenado, el caudal u otros parámetros del proceso de llenado, o sustituir las piezas desgastadas o dañadas del equipo de llenado.
Cómo manejar la máquina tapadora de husillo
Probar y verificar: Una vez ajustado el proceso de llenado o el equipo, es importante probar y verificar que el sistema de llenado produce el volumen o el peso correctos. Esto puede implicar recopilar y analizar datos adicionales o realizar una inspección visual de los envases llenos.
Es importante calibrar periódicamente el sistema de llenado para garantizar que se dispensa el volumen o peso correcto del producto. También es una buena idea establecer un programa de calibración rutinario y documentar el proceso de calibración para garantizar que el sistema de llenado produce sistemáticamente los resultados deseados.